Generative AI Powered Manufacturing Technician chatbot
Revolutionizing Efficiency and Precision
Manufacturing companies stand as the pillars of industrial progress, driving economies and
innovation forward with their unwavering commitment to quality and efficiency. At the heart of
these enterprises are technicians, the unsung heroes who ensure seamless operations,
troubleshoot challenges, and maintain the intricate machinery that powers production.
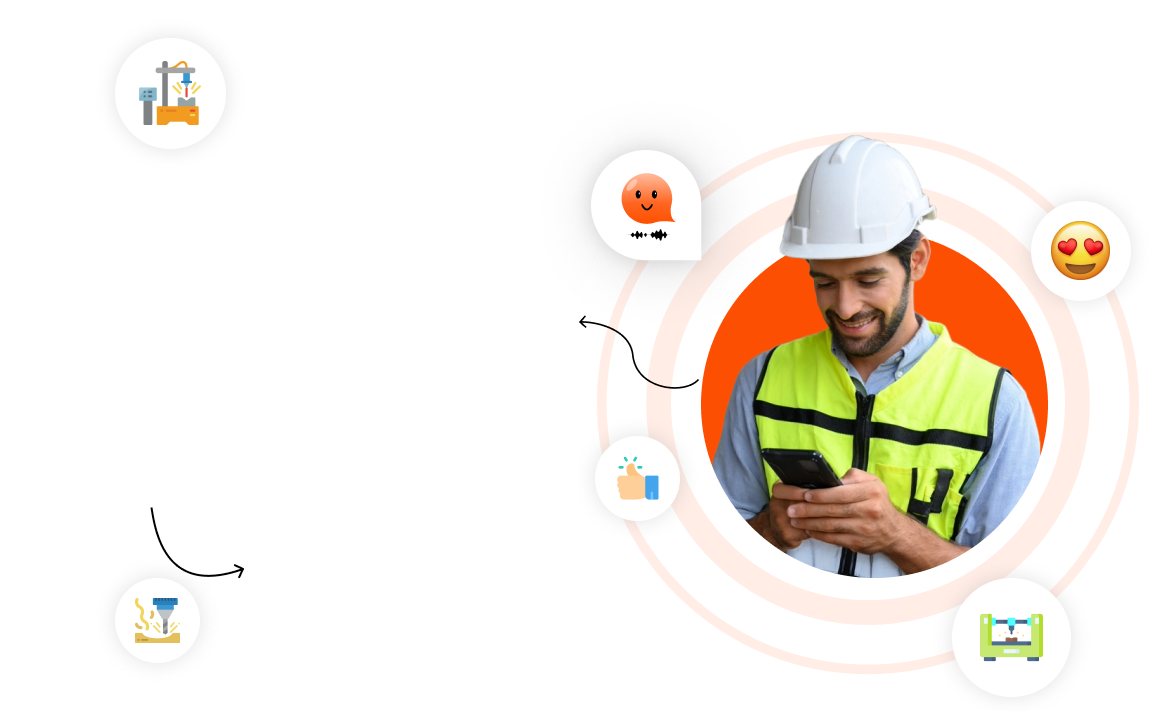
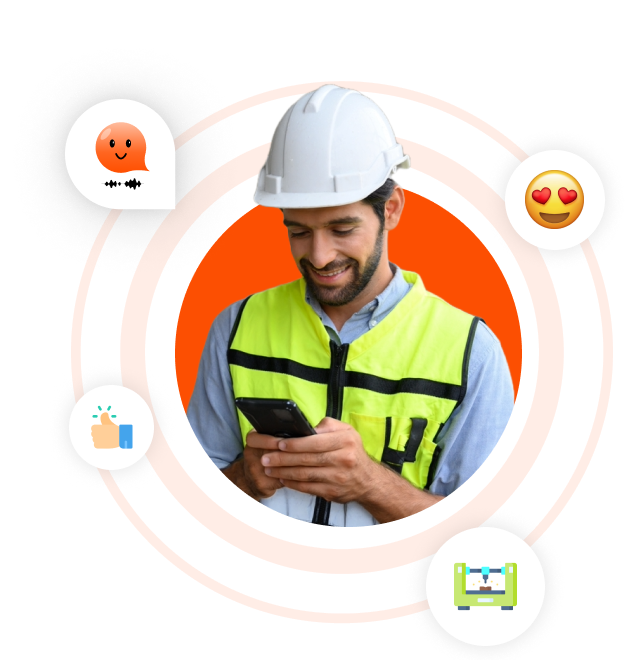
Hi, I need some help with the CNC machine. The machine is not holding the specified
tolerances.
I see. Have you calibrated the machine recently?
Yes, I calibrated it this morning, but it’s still giving me problems.
Alright! Have you checked the tool wear? Sometimes worn tools can cause dimension
inaccuracies.
I replaced the cutting wool yesterday, so it should be fine. Could be something with the
machine’s software?
However, even with their expertise, technicians often face challenges such as accessing timely
information from manuals and documentation, interpreting complex equipment schematics, and
efficiently managing troubleshooting procedures amidst tight production schedules.
Pain Points and Challenges
Technicians frequently encounter significant hurdles that impact productivity and efficiency:

67% of technicians report that they spend too much time searching
for information they need to do their jobs effectively.
– IndustryWeek
– IndustryWeek

55% of technicians find it difficult to navigate through complex
manuals and schematics to locate critical information.
– Field Technologies Online
– Field Technologies Online

45% of technicians struggle with inconsistent access to historical
data and troubleshooting procedures, leading to prolonged downtime.
– Forbes
– Forbes

63% of technicians report challenges due to a lack of specialized
skills and training required to handle modern equipment and technologies.
– Deloitte
– Deloitte
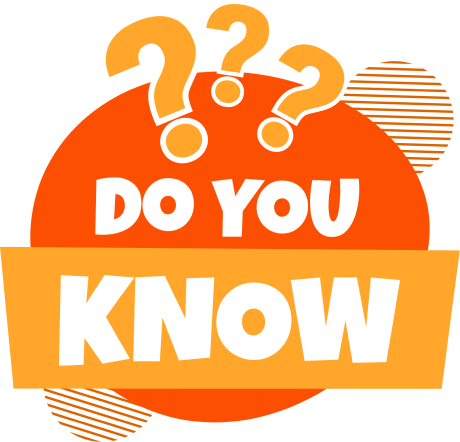
$260,000
On average, manufacturing companies lose $260,000 per hour due to unplanned downtime caused by equipment failures and maintenance delays. – PwC
On average, manufacturing companies lose $260,000 per hour due to unplanned downtime caused by equipment failures and maintenance delays. – PwC
The Solution: A Smart chatbot for Technicians with Generative AI Power
Recognizing the pressing challenges manufacturing companies and technicians face, we at Streebo,
a leading Digital Transformation & AI Company, have developed a new range of smart chatbots
tailored for manufacturing operations. These chatbots are designed to address critical pain
points such as complex troubleshooting, skill enhancement through on-demand access to training
modules,and providing data-driven insights to optimize maintenance schedules and reduce
downtime. Our chatbots are meticulously crafted to meet the unique requirements of the industry,
ensuring technicians have the tools they need to operate and maintain equipment efficiently.
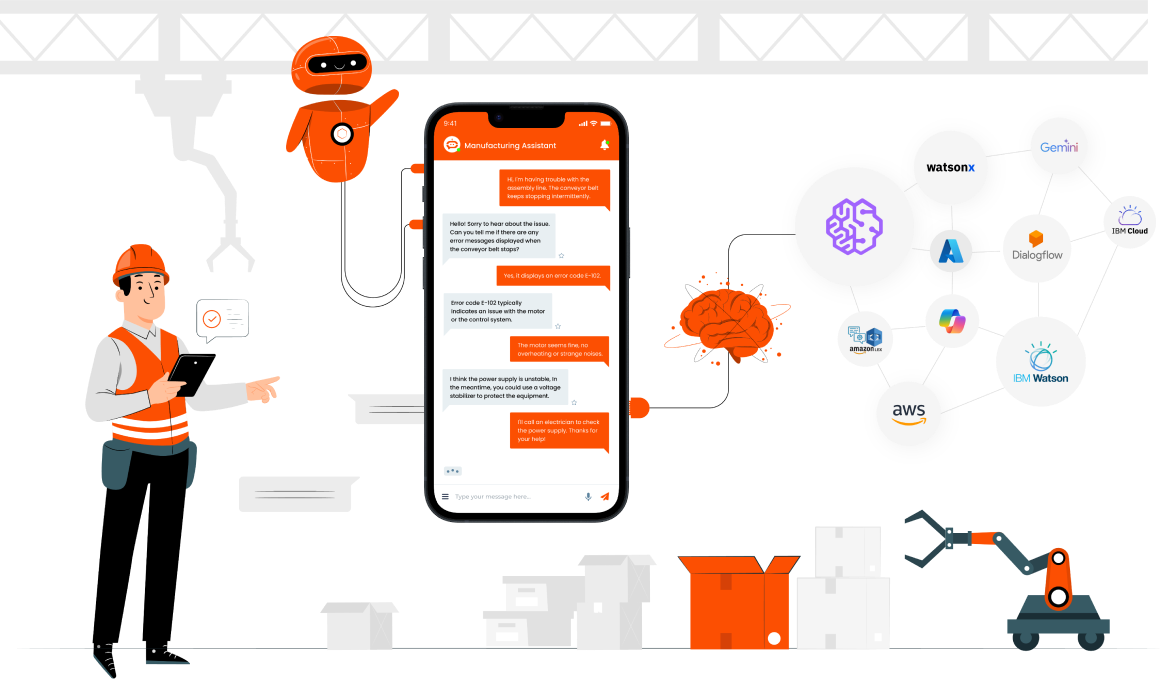
Our manufacturing bots for technicians are built on world-class NLPs and generative AI platforms
from industry leaders such as IBM, Google, Microsoft, and AWS. Utilizing Gartner-recognized NLPs
like IBM Watson, Google DialogFlow, Amazon Lex, and Microsoft Copilot, combined with advanced
generative AI technologies such as IBM Watsonx, Enterprise GPT on Azure, Google Gemini, Amazon
SageMaker, or Microsoft Copilot, our solution offers unparalleled flexibility. This allows
enterprises to choose the technology that best aligns with their business objectives, ensuring
our chatbots deliver powerful capabilities that enhance operational efficiency and support
continuous improvement initiatives.
How can it help Manufacturing Companies?
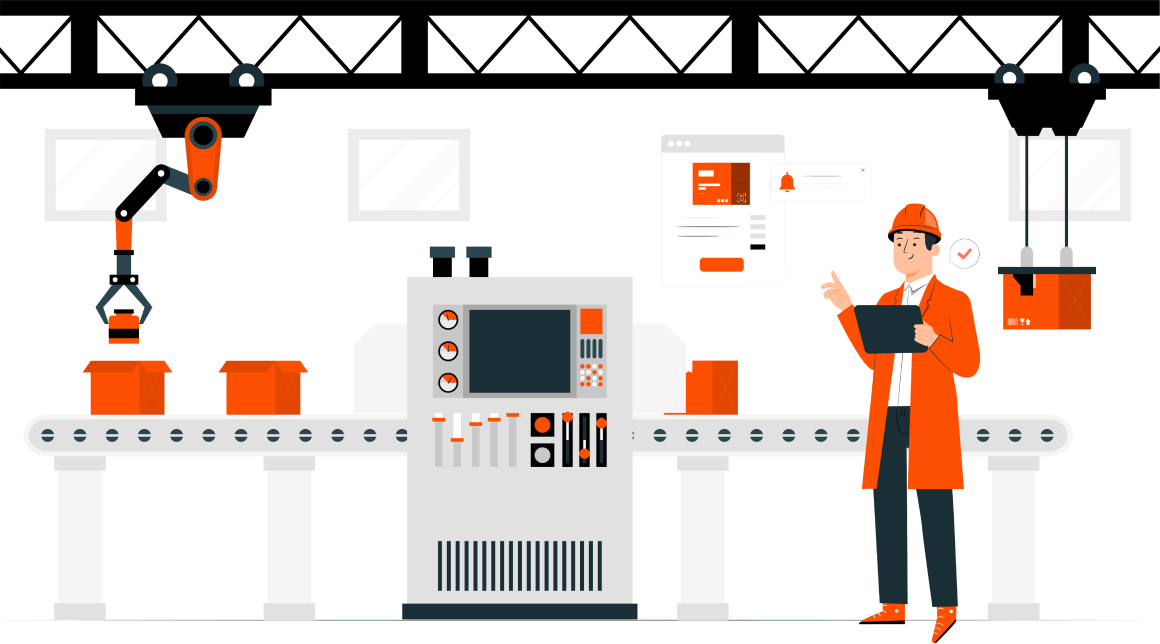
Imagine having an AI assistant that comprehensively understands every detail of your
manufacturing plant and every team member could instantly access precise information, tailored
to their role, with just a few clicks? With Manufacturing Technician chatbot, powered by
top-tier Gen AI platforms these possibilities become realities.

Smart bots autonomously learn from uploaded manuals, work orders, setup guides, and troubleshooting steps, ensuring alignment with your operational needs.

Employees interact conversationally with the chatbot to promptly and efficiently resolve issues, eliminating downtime spent searching for answers.

Engineers quickly find solutions to complex problems or retrieve design guidance for new projects, enhancing innovation and productivity.

The chatbot interprets schematics and technical details, providing insights into equipment functions and configurations. It supports multiple languages, facilitating seamless communication across global teams.

Receive instant responses to inquiries, including troubleshooting steps and design recommendations, with citations to source materials for further exploration.

Effortlessly guide technicians through step-by-step troubleshooting procedures tailored to specific alarms, minimizing downtime and maximizing productivity.

Provides real-time analysis of production metrics such as pieces produced, scrap rates, and downtime, enabling proactive decision-making to enhance operational efficiency.

Maintains comprehensive logs and detailed histories of preventive maintenance (PM), integrating seamlessly with platforms like Plex to ensure equipment reliability and operational continuity.

Associates data with specific machines, facilitating targeted diagnostics and maintenance support for quicker issue resolution and improved equipment uptime.

Supports diverse data entry methods including text, audio with transcription, video with transcription, image recognition, and OCR for images. This versatility enhances communication and documentation efficiency across all operational levels.
Practical Applications of Manufacturing Technician Bots
For Engineers



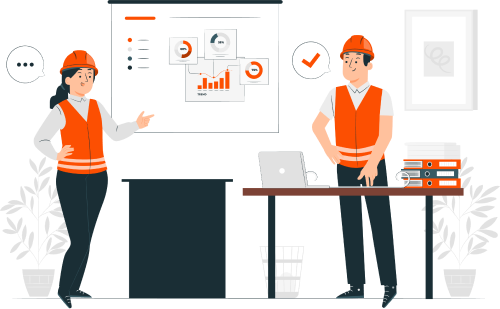
For Technicians



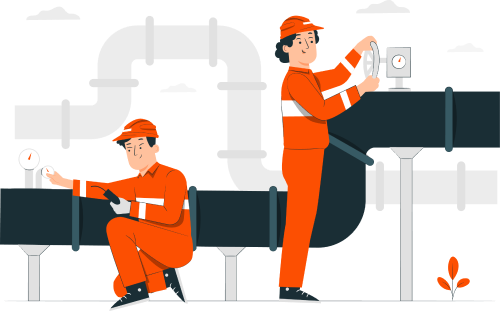
For QC Inspectors



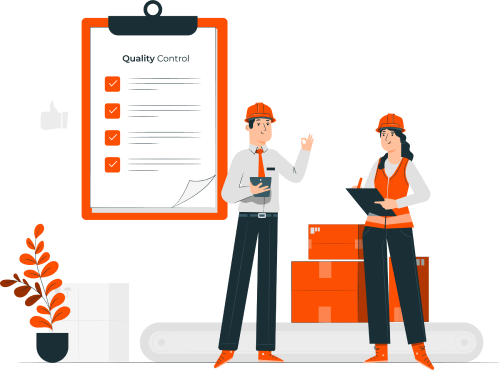
For Tooling Managers



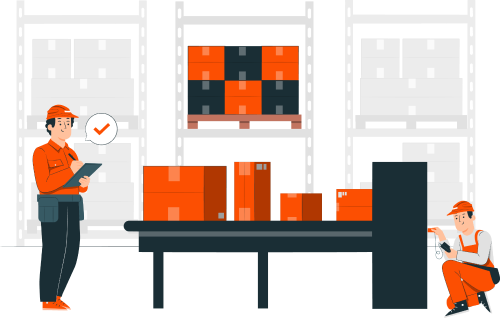
Business Benefits of Generative AI Powered Manufacturing Technician chatbot

Technicians experience a 37% increase in productivity as bots automate routine tasks and streamline workflows.
– IBM

Bots contribute to a 45% improvement in operational efficiency by optimizing resource allocation and minimizing manual errors.
– Deloitte

Companies can achieve a 25% reduction in maintenance costs due to proactive maintenance scheduling and optimized spare parts management.
– PwC

Technician Bots lead to a 30% increase in equipment uptime by providing real-time monitoring and immediate response to equipment issues.
– Aberdeen Group

Technical issues are resolved 50% faster with bots, thanks to instant access to troubleshooting guides and automated diagnostic capabilities.
– Forrester

Employees report a 40% increase in job satisfaction as bots handle repetitive tasks, allowing technicians to focus on more strategic and rewarding activities.
– Statista
How does a Generative AI-powered chatbot improve efficiency in manufacturing processes?
Documentation Needed to train the AI model
Essential








Desired



Features and Key Differentiators: What Sets Us Apart?




Supports 38+ languages to accommodate diverse global teams and facilitate clear communication and instructions.

Offers interactive training modules for technicians, enhancing skill development, onboarding efficiency, and knowledge retention.

Facilitates data input through text, audio with transcription, video with transcription, image recognition, and OCR, ensuring versatility and ease of use.

Ensures data security through robust encryption, access controls, and compliance with industry standards and regulations.

Integrates seamlessly with CRM and ERP systems to manage equipment data, service records, and inventory, enhancing operational transparency and efficiency.

Provides quick access to equipment manuals, schematics, maintenance logs, troubleshooting guides, and instructional materials for informed decision-making.

Analyzes production metrics like pieces produced, scrap rates, and downtime in real-time to optimize processes and improve operational efficiency.

Tailors workflows and processes to specific manufacturing requirements, optimizing operations and ensuring consistency in service delivery.

Supports voice interactions to facilitate hands-free operation and accessibility in noisy or complex manufacturing environments.

Centralizes equipment data, maintenance logs, and service histories for comprehensive visibility and strategic decision-making.

Offers scalable deployment options, including on-premises installation and cloud deployment, to adapt to varying organizational needs and infrastructure.

Associates data with specific machines, enabling targeted diagnostics, predictive maintenance, and personalized support for improved equipment uptime.
Pricing Options
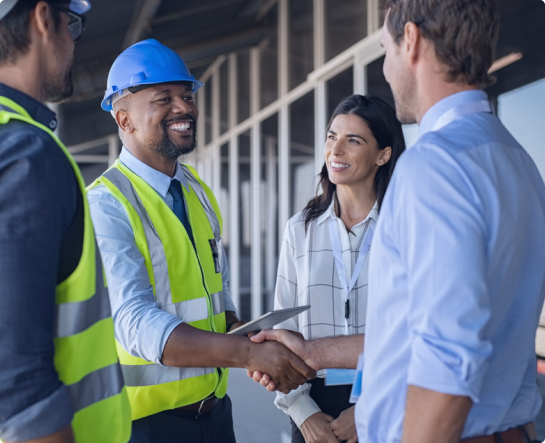

You can choose to buy the Bot solution.

You can choose to Subscribe to tour Bot solution for a fixed monthly charge

This is a conversation-based subscription and tied to the number of conversations & messages the bot handles. Thus, you only pay if the Bot is getting used and is actually deflecting calls.
Want to Know- How This Will Work for Your Business?
Explore the power of our Technician Bots in three easy steps:



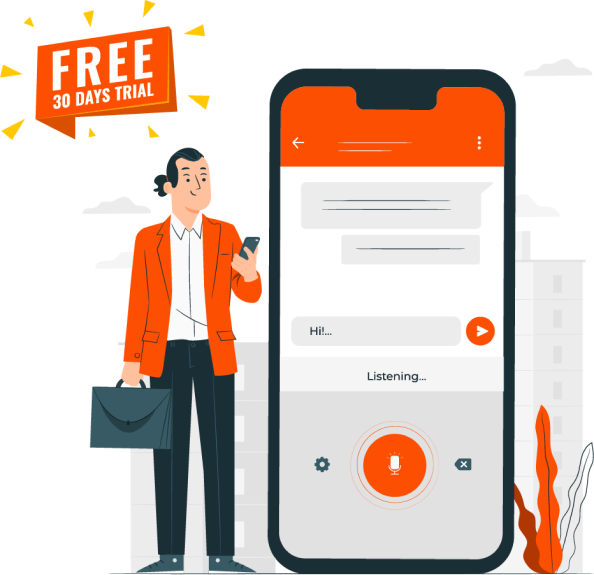